Professional sheet metal and tool handling with VENTOR. Flexible production systems and press automation are the modern range of Coiltech products.
Sheet metal shears
This is the heart of the cutting line. Depending on the section, the type of materials to be processed and the required cutting speed, pneumatic, hydraulic or mechanical shears are selected. Quality workmanship will allow minimal burrs when cutting and reduce the frequency of sharpening.
- Economical pneumatic shears are designed for fast and accurate cutting of thin and delicate metals: aluminum or polished stainless steel, copper, silicon steel, etc. They are limited to sections of less than 650 mm².
- Hydraulic shears are used for cutting heavy profiles or strips with high yield strength. They can be equipped with hydraulic pressure.
- Ultra-fast mechanical guillotine shears type 1730 with crankshaft can reach speeds of up to 200 rpm. They are designed for incorporation into production lines. The frame, which is transparent under the blades, allows direct placement of blanks without an intermediate conveyor.
Sheet end shearing
Recommended for wide or thick sheets, adding shears after a straightening machine or feeder allows the ends of sheets to be cut off in complete safety. The shear helps reduce production changeover time: it allows easier removal of the cutting tool and facilitates rewinding and splicing operations. Available in widths from 300 to 1525 mm.
Stackers
Coiltech offers an economical range of simple and efficient stackers. Stacking lengths can reach 5 m, with widths adjustable up to 2000 mm. The stacker can be supplemented with a pneumatic impulse device. The stack is built on one or more elevator tables equipped with servo control for automatic stacking at a constant level.
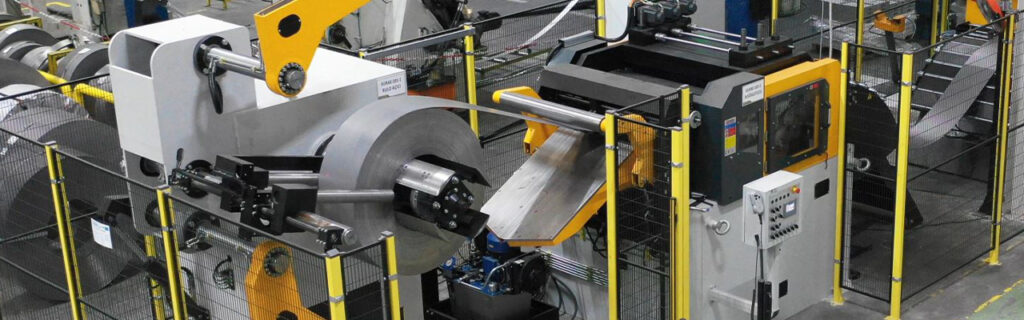